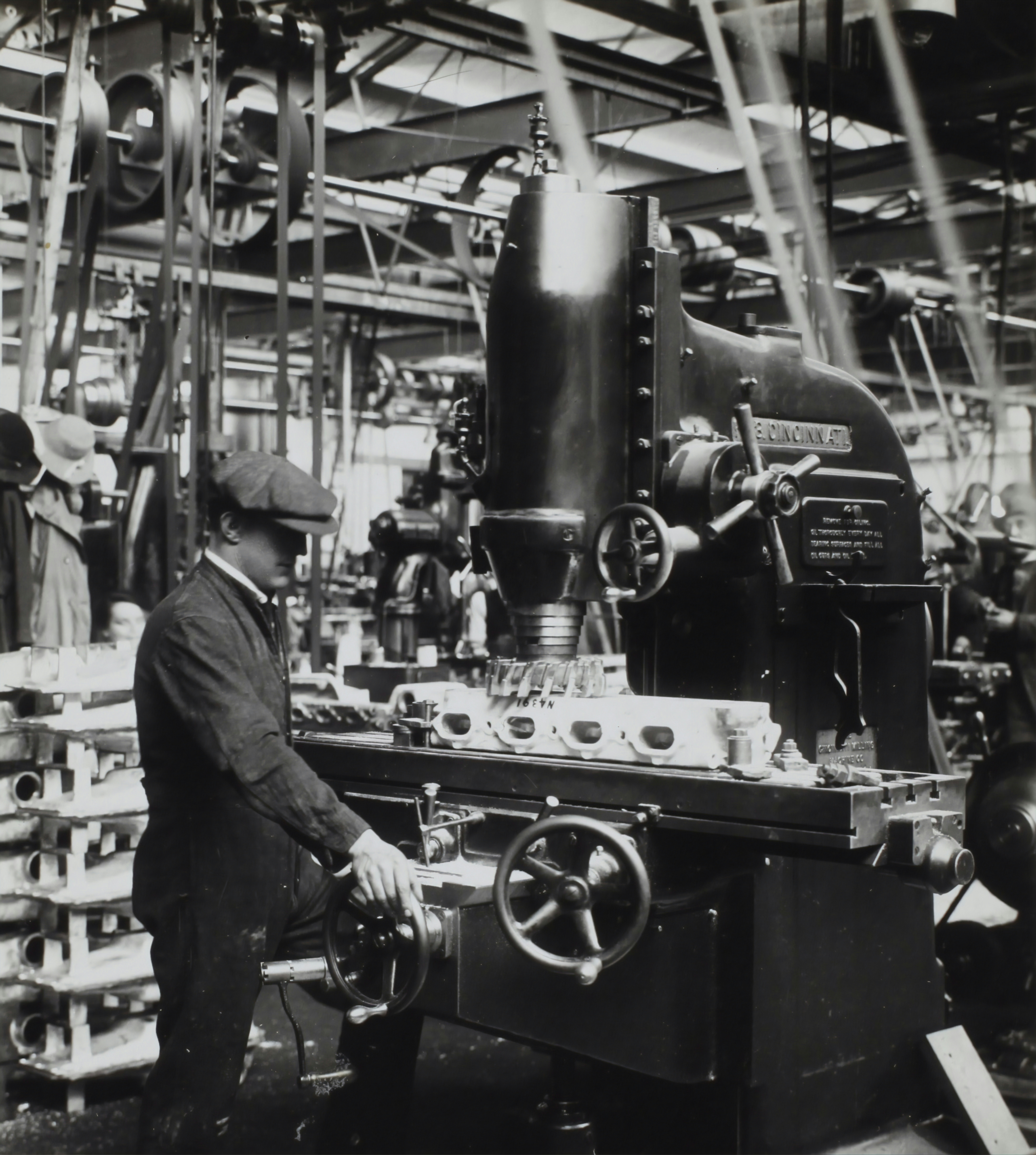
The fourth industrial revolution, known as Industry 4.0, is redefining the manufacturing landscape by integrating digital technology, automation, and data analytics. This transformation is driven by cutting-edge technologies that enhance efficiency, streamline operations, and create more intelligent, responsive production systems. Companies that embrace these innovations gain a competitive edge through increased productivity, cost savings, and improved product quality.
Manufacturers are adopting advanced technologies such as artificial intelligence (AI), the Industrial Internet of Things (IIoT), robotics, additive manufacturing, and augmented reality (AR) to optimize their processes. These innovations are reshaping traditional manufacturing and driving the industry toward an era of increased automation, sustainability, and customization.
Smart Factories and the Industrial Internet of Things (IIoT)
One of the most significant advancements in Industry 4.0 is the emergence of smart factories. These facilities leverage IIoT to connect machines, sensors, and software, creating a fully integrated production environment with minimal human intervention.
IIoT enables real-time data collection and analysis, allowing manufacturers to monitor equipment performance, track production metrics, and optimize workflows. With sensors embedded in manufacturing equipment, companies can detect inefficiencies, adjust processes on the fly, and improve overall productivity.
A significant benefit of IIoT is predictive maintenance. Traditional maintenance approaches rely on scheduled servicing or reactive repairs when a machine fails. Predictive maintenance, however, uses AI-driven data analytics to detect early signs of wear and tear, allowing manufacturers to perform maintenance before a breakdown occurs. This reduces downtime, extends equipment life, and minimizes repair costs.
IIoT also improves supply chain visibility. Manufacturers can track raw materials, inventory, and shipments in real-time, ensuring smooth operations and reducing waste. Manufacturers can make data-driven decisions to optimize supply chain management and enhance efficiency by leveraging cloud-based analytics platforms.
Artificial Intelligence and Machine Learning in Manufacturing
AI and machine learning are revolutionizing the manufacturing industry by enabling systems to analyze vast amounts of data, predict outcomes, and automate complex decision-making processes. These technologies improve efficiency, quality control, and customization in production environments.
One of AI’s most valuable applications in manufacturing is quality assurance. AI-powered computer vision systems can inspect products for defects with remarkable accuracy. These systems analyze images from production lines, identifying inconsistencies or flaws that might go unnoticed by human inspectors. This reduces waste and ensures that only high-quality products reach consumers.
AI-driven predictive analytics also play a key role in demand forecasting. AI can predict demand fluctuations and adjust production schedules by analyzing historical data, market trends, and consumer behavior. This prevents overproduction, reduces excess inventory costs, and enhances supply chain resilience.
Additionally, AI is being used to optimize manufacturing workflows. AI algorithms analyze production data to identify inefficiencies and recommend process improvements. This helps manufacturers streamline operations, reduce energy consumption, and maximize resource utilization.
Robotics and Automation in Manufacturing
Automation has been a staple of manufacturing for decades, but advancements in robotics are making production lines faster, more precise, and more adaptable than ever before. The rise of collaborative robots (cobots) and autonomous mobile robots (AMRs) is changing how factories operate.
Industrial robots are commonly used for welding, assembly, painting, and packaging tasks. These robots can perform repetitive tasks with precision and speed, reducing human error and increasing productivity. Unlike traditional robotic systems that require extensive programming, modern AI-powered robots can learn and adapt to new tasks, making them more versatile.
Cobots are designed to work alongside human workers, enhancing productivity without replacing human labor. Unlike conventional industrial robots, cobots have advanced sensors and AI algorithms to detect human presence and adjust their movements accordingly. This ensures a safer working environment while increasing efficiency.
AMRs are transforming logistics and material handling within factories. Unlike automated guided vehicles (AGVs), which follow fixed paths, AMRs use AI and sensors to navigate autonomously. These robots transport raw materials, components, and finished goods throughout production facilities, reducing the need for manual labor and improving operational efficiency.
Additive Manufacturing and 3D Printing
Additive manufacturing, commonly known as 3D Printing, is revolutionizing how products are designed, prototyped, and manufactured. Unlike traditional subtractive manufacturing methods, which remove material to create a final product, additive manufacturing builds objects layer by layer, minimizing waste and enabling more complex designs.
One of the most significant advantages of 3D Printing is rapid prototyping. In the past, creating prototypes required expensive molds and tooling, which extended development cycles. With 3D Printing, manufacturers can quickly produce prototypes, test designs, and make modifications without costly rework. This accelerates innovation and shortens the time-to-market for new products.
Beyond prototyping, 3D Printing is increasingly being used for full-scale production. Industries such as aerospace, automotive, and healthcare are leveraging additive manufacturing to produce lightweight, high-performance components. Advances in 3D printing materials, such as metal alloys, carbon fiber composites, and biocompatible polymers, are expanding the applications of this technology.
Another key benefit of 3D Printing is its potential to enable localized and on-demand manufacturing. Instead of relying on centralized factories and extended supply chains, companies can print parts closer to their point of use, reducing transportation costs and lead times. This is particularly valuable for spare parts manufacturing, where 3D Printing eliminates the need for extensive inventories.
Augmented Reality (AR) and Virtual Reality (VR) in Manufacturing
AR and VR are emerging as valuable tools in modern manufacturing, enhancing training, maintenance, and design processes. These immersive technologies provide workers with real-time information and interactive experiences that improve efficiency and reduce errors.
AR is widely used for maintenance and troubleshooting. AR-enabled smart glasses or tablets overlay digital instructions onto physical equipment, guiding technicians step by step through complex repair procedures. This reduces reliance on printed manuals and minimizes downtime.
In workforce training, VR creates realistic simulations that allow employees to practice operating machinery, assembling products, or handling hazardous materials in a virtual environment. This hands-on approach improves learning retention and prepares workers for real-world scenarios without the risks associated with on-the-job training.
AR is also revolutionizing product design and prototyping. Engineers can use AR to visualize 3D models of products in real-world environments, making it easier to evaluate designs before production begins. This improves collaboration between design teams and reduces costly design errors.
As AR and VR technologies continue to evolve, their applications in manufacturing will expand, improving productivity, safety, and decision-making across the industry.
Industry 4.0 transforms manufacturing through cutting-edge technologies that enhance automation, efficiency, and flexibility. Integrating IIoT, AI, robotics, additive manufacturing, and AR/VR is revolutionizing how manufacturers operate, enabling data-driven decision-making and intelligent production systems.
Smart factories powered by IIoT optimize workflows, predictive maintenance reduces downtime, and AI-driven automation improves quality control. Robotics enhances speed and precision in manufacturing, while 3D Printing enables rapid prototyping and on-demand production. Meanwhile, AR and VR are revolutionizing training, maintenance, and design processes.
As Industry 4.0 continues to evolve, manufacturers that embrace these innovations will gain a competitive advantage, improving efficiency, reducing costs, and responding quickly to market demands. The future of manufacturing is digital, intelligent, and highly connected, paving the way for a new era of industrial excellence.