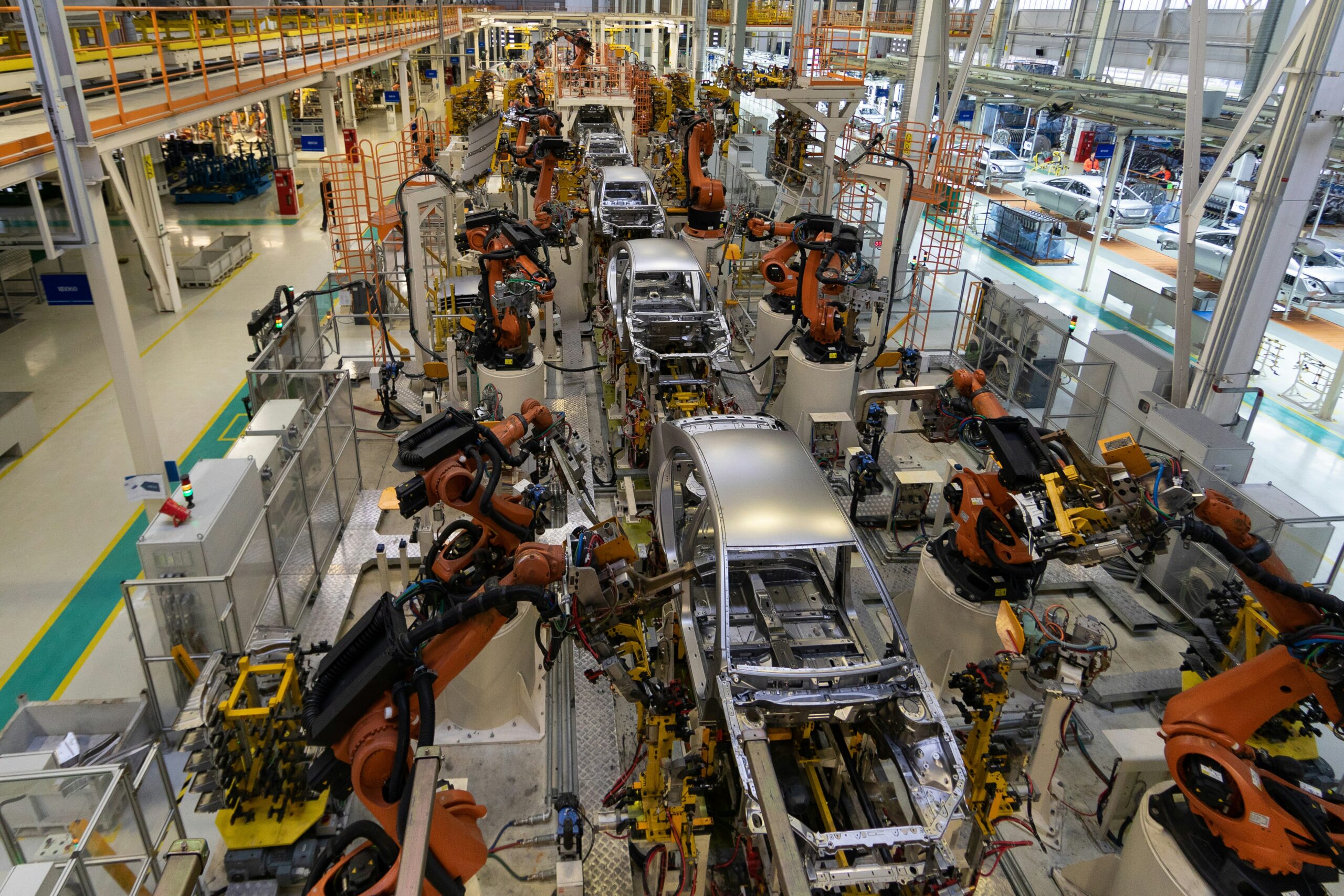
As environmental challenges become more urgent, industries worldwide are rethinking their operations. The manufacturing sector is a significant contributor to environmental degradation and a powerful force for change. Fortunately, with the rise of advanced technology, manufacturers are finding new ways to shrink their ecological footprint while boosting productivity. This shift toward sustainable manufacturing is not just a moral choice—it’s becoming a competitive advantage.
Modern technology is helping manufacturers move beyond traditional, waste-heavy processes toward more innovative, cleaner methods. As a result, the future of manufacturing is being shaped by tools and strategies designed to reduce waste, conserve energy, and use resources more efficiently. With a combination of innovation, data, and automation, companies find that sustainability and profitability can go hand in hand.
Digital Tools Turn Data into Action
One of the most transformative elements of sustainable manufacturing is the ability to use data to drive real-time decision-making. Thanks to the development of smart sensors, cloud computing, and industrial analytics platforms, manufacturers now have access to a constant stream of operational data. This information reveals how materials, energy, and machines are used—and where improvements can be made.
For example, if a factory sees that one of its machines consumes significantly more power than others, it can investigate the cause and either repair or replace the machine. Similarly, real-time data can help operators adjust parameters immediately if production processes create excess material waste. Rather than relying on reactive problem-solving, companies use proactive strategies to minimize inefficiencies before they escalate.
Precision Manufacturing Cuts Material Waste
Reducing raw material waste is a core goal of any sustainable production strategy. Companies are turning to precision technologies such as laser cutting, CNC machining, and digital fabrication tools to meet this goal. These machines can execute highly accurate cuts and measurements, significantly reducing the excess material that would traditionally be discarded.
Additionally, digital modeling tools allow engineers to simulate production runs before they occur. By identifying and correcting potential flaws early in the process, manufacturers can prevent unnecessary material use and reduce the likelihood of producing defective parts. With better control over inputs, companies reduce waste, save money, and lower the environmental costs of sourcing materials.
3D Printing Changes the Game
Additive manufacturing, better known as 3D printing, is revolutionizing product production. This technique builds objects layer by layer, using only the necessary material. Compared to traditional methods that carve or cut from larger blocks, 3D printing virtually eliminates the creation of scrap material.
Furthermore, 3D printing supports localized, on-demand production. Instead of shipping parts across continents and keeping extensive inventories, companies can print parts close to the point of use. This reduces transportation emissions and storage needs, adding another layer of sustainability to the manufacturing process. As materials and printing technologies continue to improve, 3D printing will become an even more critical tool for eco-friendly production.
Smarter Energy Management in Factories
Energy efficiency is another area where technology is making a significant impact. Manufacturing facilities are among the biggest energy consumers in the world, but intelligent systems are helping companies reduce their usage and shift toward renewable sources. Smart grids, automated controls, and energy-monitoring software allow companies to understand where energy is consumed and how to optimize it.
For example, intelligent systems can automatically power down machines during inactivity or schedule energy-intensive tasks for off-peak hours when grid demand is lower. These adjustments not only reduce costs but also lower greenhouse gas emissions. Additionally, many manufacturers are now generating clean power onsite by integrating solar panels, wind turbines, or geothermal systems to meet part of their energy needs.
Internet of Things (IoT) Enhances Efficiency
The Internet of Things (IoT) is critical in making manufacturing more sustainable. Manufacturers gain detailed insight into how each system component performs by connecting machines, tools, and infrastructure through smart sensors and devices. This visibility leads to faster identification of inefficiencies, maintenance needs, and environmental impact.
Take, for example, a refrigeration system used in food manufacturing. With IoT sensors, the company can monitor temperature, humidity, and energy consumption around the clock. If something goes wrong—such as a temperature spike that threatens product quality—the system can automatically alert managers or adjust settings in real-time. This intelligent monitoring reduces waste, prevents spoilage, and helps companies meet regulatory standards.
Designing Products with Sustainability in Mind
Sustainability doesn’t start on the factory floor—it begins in the design phase. Engineers use powerful software to develop products that are easier to manufacture, use fewer materials, and generate less waste throughout their life cycle. This process, called eco-design or sustainable design, is becoming a core part of product development.
With digital modeling and simulation tools, teams can test how different materials, shapes, or production methods affect performance and sustainability. This allows companies to make informed decisions before physical production begins, cutting down on trial-and-error waste. As consumers become more eco-conscious, sustainable design becomes a valuable selling point for businesses that want to stand out.
Supporting a Circular Economy
Technology also empowers manufacturers to transition from linear to circular economies. In a circular model, products and materials are reused, remanufactured, or recycled instead of discarded. To make this work at scale, manufacturers are adopting digital tracking systems that monitor products from cradle to grave.
For instance, companies can embed tracking codes in components that allow them to be identified and returned at the end of use. Once back in the system, these components can be refurbished or recycled for future use. With the help of blockchain, cloud storage, and machine learning, circular systems are becoming more reliable and accessible. This shift not only conserves resources but also reduces the amount of waste sent to landfills.
Collaboration is Key to Long-Term Success
Lastly, sustainable manufacturing requires collaboration. Whether it’s sharing data with suppliers, partnering with clean energy providers, or co-developing solutions with research institutions, manufacturers realize they can’t do it alone. Fortunately, digital platforms and cloud technologies make it easier than ever to work across organizational boundaries.
Companies can set industry-wide sustainability benchmarks through collaboration, accelerate innovation, and scale best practices. These partnerships often lead to breakthroughs in cleaner production methods, improved material use, or energy alternatives that benefit everyone involved. As sustainability becomes more ingrained in business strategies, collaboration will continue to drive lasting change.
Sustainable manufacturing is no longer an idealistic vision—it’s an achievable reality powered by technology. From real-time data analysis to intelligent energy systems and circular design, innovation enables industries to produce more responsibly. While the transition requires investment and commitment, the rewards—greater efficiency, reduced waste, and a healthier planet—are well worth the effort. As more manufacturers embrace these tools and strategies, they will lead in building a more sustainable future for all.