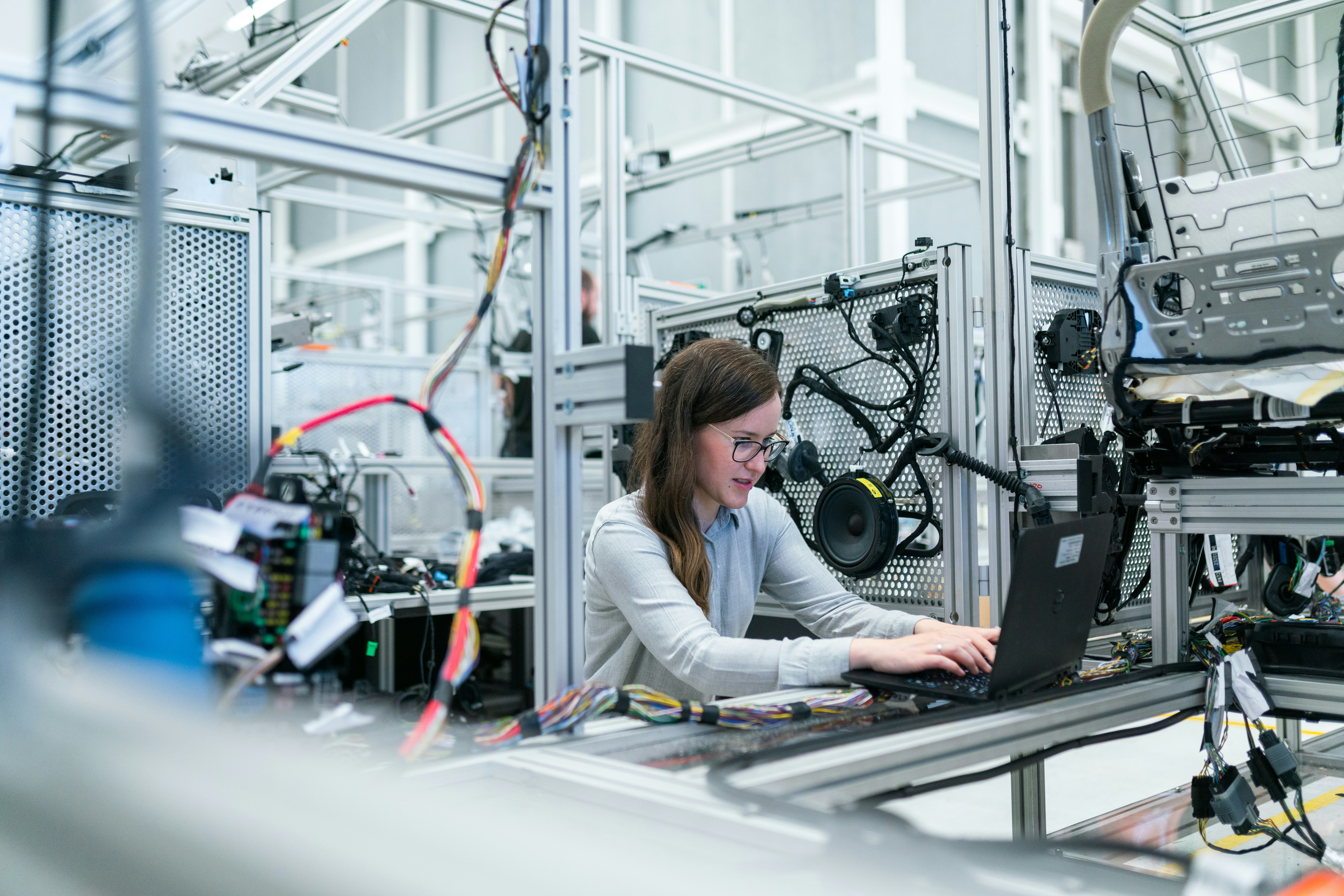
Manufacturing technology has significantly transformed industries’ operations, driving productivity, efficiency, and quality. Adopting advanced technologies has become crucial as companies strive to stay competitive in an increasingly globalized market. From automation to artificial intelligence (AI), these innovations streamline production processes and open the door for more sustainable and customized manufacturing solutions.
In today’s world, technology is no longer just an enhancement; it’s a game-changer. Let’s explore how manufacturing technology shapes the future of production across various industries.
The Impact of Automation in Manufacturing
Automation has been at the forefront of manufacturing technology, revolutionizing the speed and precision with which products are made. By automating repetitive tasks, companies can drastically reduce human error and increase throughput. Additionally, automation allows for round-the-clock operations, further boosting efficiency. Automation has become indispensable in industries like automotive manufacturing, where precision and scale are key. For example, robotic arms are used extensively for welding, painting, and assembly, ensuring consistent quality and speed.
Moreover, automation helps companies maintain flexibility in their production lines. With the integration of innovative technologies, manufacturers can quickly reconfigure their systems to accommodate new product designs or changes in production demand. This adaptability has proven essential in the fast-paced market, allowing manufacturers to respond to customer needs more swiftly than ever.
Artificial Intelligence: Enhancing Decision-Making in Manufacturing
Artificial Intelligence (AI) is increasingly being utilized to enhance decision-making processes in manufacturing. With its ability to analyze vast amounts of data, AI can predict maintenance needs, optimize supply chains, and improve product quality. For instance, AI-driven predictive maintenance systems can identify potential failures in machinery before they occur, reducing downtime and maintenance costs. This saves money and helps maintain a continuous flow of production.
Additionally, AI assists in optimizing production schedules by analyzing data from multiple sources, such as production rates, inventory levels, and customer orders. By doing so, AI can suggest the most efficient way to allocate resources and manage production, leading to cost savings and faster product-to-market time. As a result, AI is helping companies operate more efficiently while making data-driven decisions that improve overall performance.
3D Printing: Revolutionizing Prototype and Part Production
The rise of 3D printing technology has been a game-changer for prototyping and part production. Unlike traditional manufacturing processes, 3D printing creates complex, customized parts directly from digital designs, eliminating the need for molds or tooling. This process, known as additive manufacturing, builds objects layer by layer, which makes it possible to produce intricate geometries that would be difficult or impossible to achieve through traditional methods.
Furthermore, 3D printing offers significant advantages in terms of speed and cost-effectiveness. Prototypes can be created in a fraction of the time it would take using traditional techniques, allowing designers to test and refine their ideas quickly. For low-volume production, 3D printing eliminates the need for expensive molds and tooling, making it a more affordable option for producing specialized parts or limited-run products. As a result, industries like aerospace, healthcare, and automotive have adopted 3D printing to create everything from lightweight components to customized medical implants.
The Role of the Internet of Things (IoT) in Smart Manufacturing
The Internet of Things (IoT) has ushered in the era of smart manufacturing, where machines, devices, and sensors are connected to the Internet and communicate in real time. IoT enables manufacturers to gather and analyze data from equipment, production lines, and even supply chains, offering valuable insights into the status of operations. For example, IoT sensors can monitor machine performance, detect inefficiencies, and trigger alerts when a machine requires maintenance.
By integrating IoT into their operations, manufacturers gain greater visibility and control over their operations. The real-time data provided by IoT devices allows businesses to make more informed decisions, improve resource allocation, and reduce waste. Moreover, IoT technology supports the development of smart factories, where automation, AI, and connected systems work together seamlessly to create a highly efficient production environment. This interconnectedness is paving the way for more intelligent, sustainable manufacturing practices.
Sustainability and Green Manufacturing Practices
As environmental concerns become more pressing, manufacturers are turning to green practices that minimize waste, conserve resources, and reduce energy consumption. Companies are integrating technologies such as energy-efficient machinery, sustainable materials, and waste reduction systems into production processes to help meet sustainability goals.
.For example, advanced technologies in energy management allow manufacturers to monitor and optimize energy use, reducing operational costs and environmental impact. Some companies are even working toward achieving carbon-neutral production by utilizing renewable energy sources like solar or wind power. These efforts benefit the environment and improve a company’s reputation and marketability as consumers increasingly demand sustainably produced products.
In addition to energy savings, sustainable manufacturing practices focus on reducing material waste by recycling and reusing raw materials whenever possible. In a world that is becoming more conscious of environmental issues, embracing green technologies is crucial for manufacturers who want to stay competitive while supporting sustainability.
The Future of Manufacturing Technology
As manufacturing technology continues to evolve, companies are embracing innovations that were once considered science fiction. The future of manufacturing holds exciting possibilities, from fully autonomous factories to the integration of virtual reality (VR) and augmented reality (AR) for design and training. These advancements promise to improve efficiency further, reduce costs, and create new business opportunities.
However, as with any technological shift, adopting these innovations comes with challenges. Manufacturers must invest in new infrastructure, upskill their workforce, and navigate potential cybersecurity risks. Despite these challenges, the benefits of embracing cutting-edge technologies are apparent. In the coming years, we can expect to see even more groundbreaking developments in manufacturing, reshaping industries, and creating new opportunities for growth and innovation.
Manufacturing technology has become a critical driver of innovation, efficiency, and sustainability. With automation, AI, 3D printing, IoT, and green manufacturing practices leading the way, the future of production looks brighter than ever. As companies adopt and integrate these technologies, they will better equip themselves to meet the demands of a fast-paced, ever-changing market, creating faster, more affordable, and more sustainable products. The evolution of manufacturing technology has just begun, and its impact will ripple across industries for years to come.